研究紹介
変形加工学研究室について
本研究室は2016年10月に発足しました.主に日本の”ものづくり”の基盤技術である塑性加工,塑性工学に関連する“材料の変形”をテーマにした変形加工学に関する研究を行っています.
本研究室のキーワードである“塑性”とは,材料にある限度以上の変形を加えるとゴムのように元の形に戻らず永久変形を生じる現象のことです. この“塑性”を利用した材料加工法を塑性加工と言い,材料を無駄にしない非常に重要な技術です. 本研究室では,材料の永久変形に着目し,主に金属材料を中心にプレス成形,チューブフォーミング,材料モデリング, また金型を使わない塑性加工技術であるダイレスフォーミングやマイクロ塑性加工に関する研究開発とその応用について,実験および理論研究を行っています.
また国際的な共同研究にも力を入れており,ロシア科学アカデミー(ロシア),ウーロンゴン大学(オーストラリア),東北大学(中国),AGH科学技術大学(ポーランド),チェコ工科大学(チェコ),ニューハンプシャー大学(アメリカ)と各種共同研究を行っています.
以下に主な研究の概要について紹介します.
主な研究テーマ
1. 金属箔材の微細精密プレス成形に関する研究
近年,医療,電子機器分野の発展に伴い,それらに用いられる成形品のさらなる微小化・高精度化が求められています. そのためそれらを成形するプレス成形にもマイクロ化・高精度化が求められています.
しかしながら,様々な寸法効果により,ただ単純にプレス成形のスケールを小さくすれば良いというわけにはいきません. 例えば,板材表面の表面粗さに着目すると,マイクロ化により被加工材の板厚が1/100になったとしても,表面粗さは1/100にはなりません. すなわちマイクロスケールにおける微細精密プレス成形では,板厚に対する表面粗さの割合が相対的に大きくなります. そのため,表面粗さが板厚の不均一性となって,早期破壊を引き起こしたり,金型との接触において表面粗さの存在がプレス成形性自体に大きな影響を及ぼすことが考えられます. また同様の問題が,結晶組織にも当てはまり,材料寸法に対する結晶粒径の影響も大きくなることが考えられます.
これらの問題に対し,微細精密プレス成形の実験,結晶粒径や表面粗さを考慮した材料モデルの構築,これらを考慮した破壊・成形限界に関する検討を行っています.
金属箔材の微細精密プレス成形に関する研究
微細精密プレス成形のために卓上型の小型サーボ式プレス機を開発しました.任意の加工モーションを実現することができます. また超小型の金型を用いてプレス成形実験を行っています.最も基本的な円筒深絞り成形により,蟻よりも小さな直径0.5mmのカップの成形に成功しています. また共焦点レーザ顕微鏡により表面あれ進展の評価を行い,材料寸法に対する表面粗さが,しわ発生や破壊等のプレス成形性に及ぼす影響を明らかにしています.
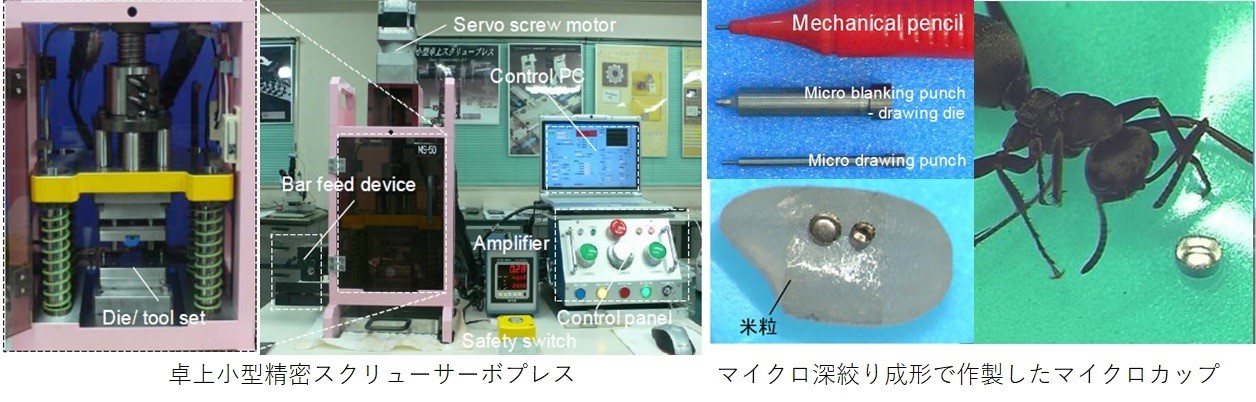
結晶粒径や表面粗さを考慮した材料モデルの構築
微細精密プレス成形のスケールでは,材料寸法に対する表面粗さおよび結晶粒径の影響を大きくなります. さらに塑性変形中の表面粗さは,金型と接触していない自由表面において,変形に伴い表面粗さが大きくなる“表面あれ現象”が生じます. ただでさえ,材料寸法に対して影響度の大きい表面粗さが加工中に増大することにより,自由表面では表面粗さの増大により破壊の起点になったり,金型と接触・摺動する場合は,接触挙動に大きな影響を及ぼすことが考えられます. “表面あれ”の原因は,金属材料が,一つ一つ異なる特性(結晶方位)を持った結晶粒によって構成されていることに起因します. 特に微細精密プレス成形のようなマイクロスケールにおける塑性変形において,結晶粒の持つ特性のばらつきによって顕著な不均一な変形が起こり,それが“表面あれ現象”となって現れることが知られています. 本研究では,有限要素解析(FEM)の中に,結晶粒単位の不均質性を考慮し,微細精密プレス成形中の表面あれ進展挙動を予測することに成功し,それらが接触挙動や成形性に及ぼす影響を明らかにしています. 本研究はJSPS二国間共同研究の支援のもと,ロシア科学アカデミー(ロシア)と共同で行っています.
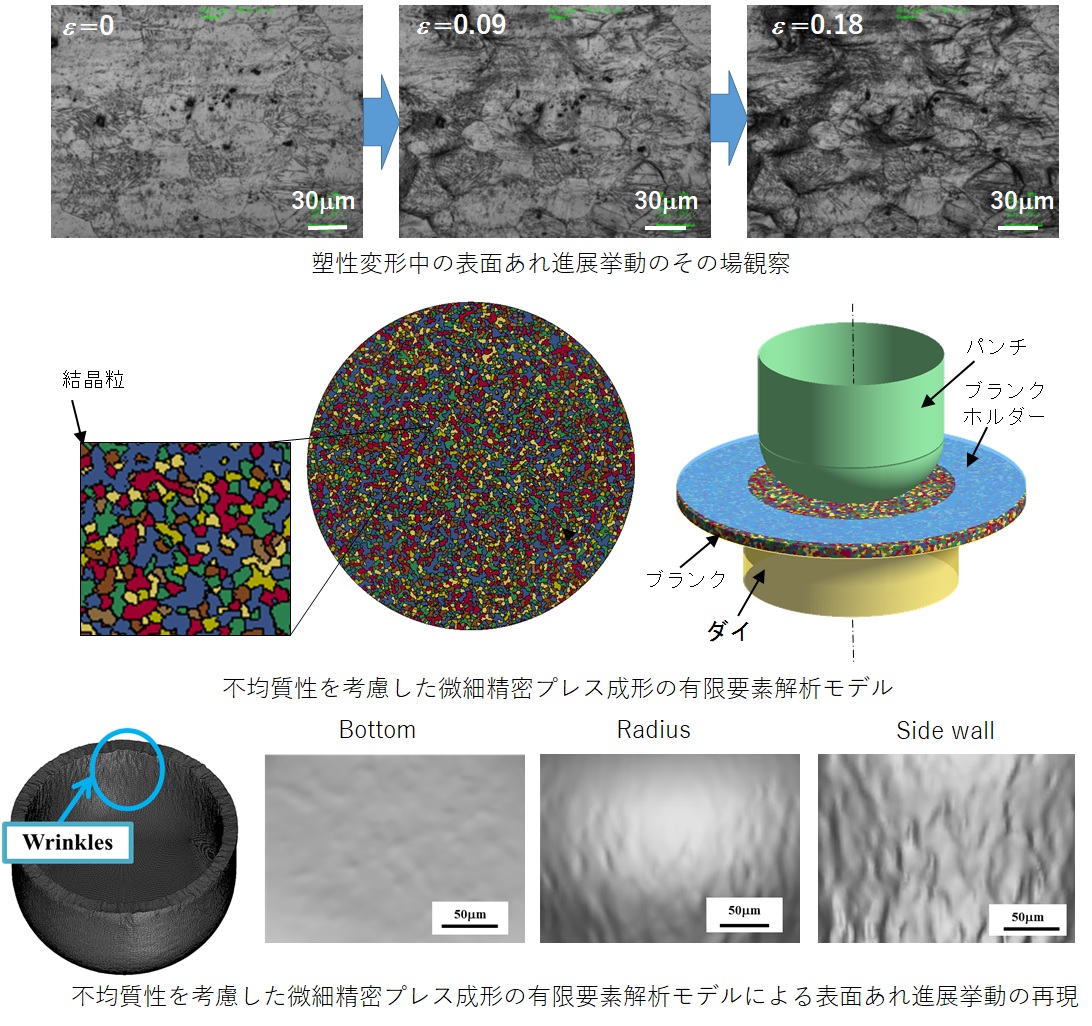
表面あれ進展挙動の顕微鏡下その場観察と可視化
本研究では,その場観察可能な小型張出試験機を開発することによって,二軸の引張変形下における表面あれ進展挙動のひずみ分布の関係を可視化することに成功しました. 手のひらサイズの超小型のMarciniak試験機を共焦点レーザ顕微鏡や3次元計測器の上に設置することで,これまで見ることができなかった,様々なひずみ状態における表面あれ進展挙動を捉えることができるようになりました. さらに局所くびれと破壊の表面プロファイルの時々刻々の変化を詳細に観察することによって,金属箔材の破壊メカニズムを明らかにしようとしています. 局所くびれと破壊の表面プロファイルの時々刻々の変化を詳細に観察することによって,金属箔材の破壊メカニズムを明らかにすることを目指しています. 金属箔材の表面あれ進展と破壊挙動を可視化することで破壊メカニズムやその破壊条件を導出することができれば,医療・電気電子機器を成形する微細精密プレス成形における寸法効果の解明や変形挙動・成形性を高精度に予測することが可能であると考えられます. 本研究はJKAの競輪の補助を受けて実施しました.
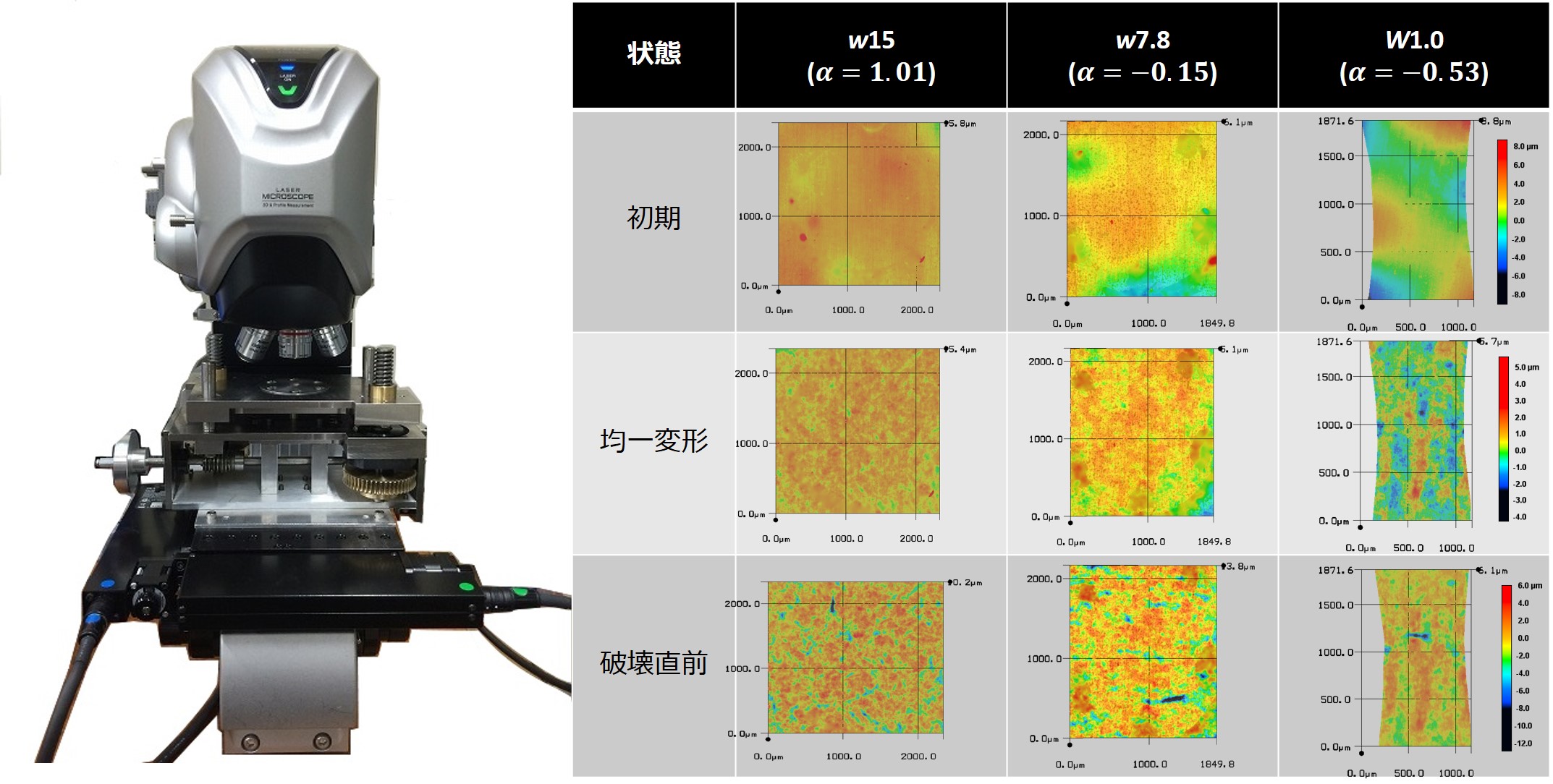
2. 金型を使わないダイレスフォーミングに関する研究
一般的な塑性加工は,必ず金型・工具を使って材料を所望の形状に変形させることによって加工を行います. しかし,近年の多品種少量生産のようなものづくりの場合,高価な金型を作ることが必ずしも必要ではない場合が存在します. そのためなるべく金型を使わずに所望の形状を得るための塑性加工法,すなわちダイレスフォーミングが注目されています. 塑性加工法において金型をなくすメリットは,他にもあります. 例えば,金型を作るのが難しい非常にマイクロな部品の成形であったり,一般的な金型では耐えられないような超高温でしか変形できない材料を,金型を使わずに塑性加工する場合に有効です. 本研究では,金型を使わずに所望の形状を加工する究極の塑性加工法であるダイレスフォーミングの開発を行っています.
ダイレス引抜きによる金属マイクロチューブの創製に関する研究
金属マイクロチューブは,無痛注射針やマイクロノズル,放電加工用電極管等,医療,化学,電子機器分野で広くニーズがある微小中空部材です. しかしながら,金属マイクロチューブのような微小中空部材を従来の金型を用いた冷間引抜きで作ろうとすると,それに用いる金型も微小なものが必要になります. そこで本研究では,金型を使わずに局部加熱と引張変形によってチューブを微小化するダイレス引抜き法を開発しました. 局部加熱するための加熱源として材料,寸法に応じて高周波誘導加熱,レーザ加熱方式を選択できるダイレスフォーミング装置を開発しています. これまでにZn-22Al超塑性合金,SUS304ステンレス鋼,βチタン等の様々な金属マイクロチューブの創製に成功しています. また単円管だけでなく,横断面の幾何学的形状が引抜き前後で変わらない特徴を活かして日の字形状等の異形管のマイクロ化にも成功しています.
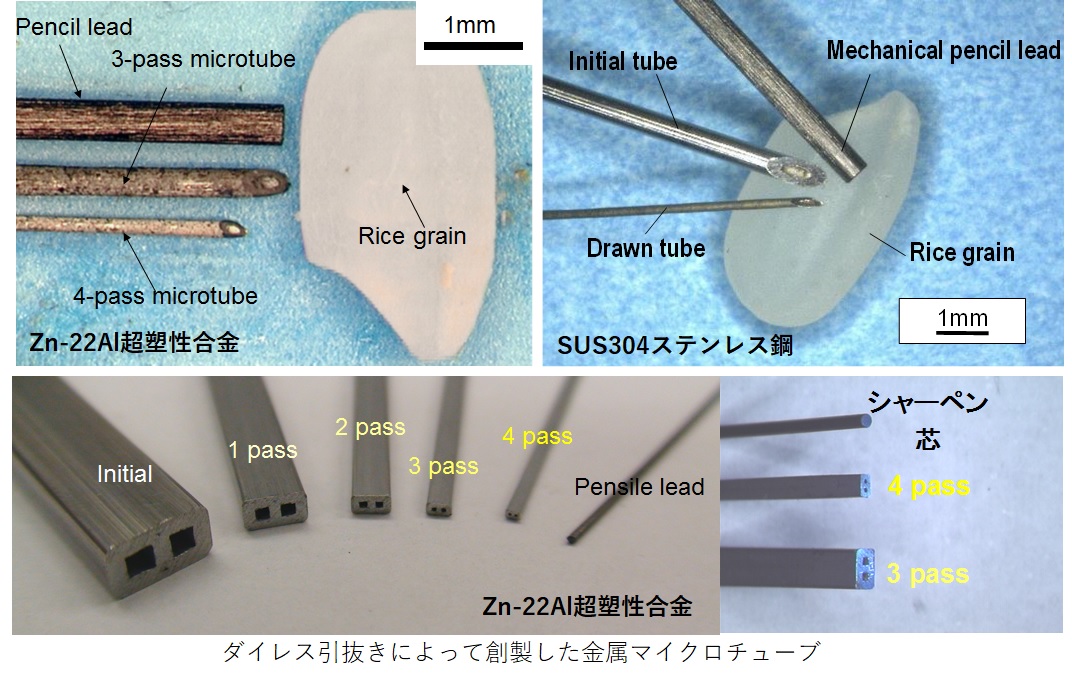
ダイレス引抜きによるマグネシウム合金管の細管化と結晶組織制御に関する研究
ダイレス引抜きは,加熱と冷却,そして塑性変形が含まれる加工プロセスです. そのため,加工温度や冷却速度,塑性変形量(ひずみ量),ひずみ速度などを制御することによって引抜き後の結晶組織を制御できると考えられます. 本研究では,医療用の生体吸収性マグネシウム合金に着目し,ダイレス引抜きを適用し,一般的な冷間引抜きでは5%程度の断面減少率を大幅に向上させた断面減少率60%を達成しながらも,結晶組織を制御できる可能性を示しています. 本研究は,JST戦略的共同研究(SICORO)の支援のもとAGH科学技術大学(ポーランド)とチェコ工科大学(チェコ)と共同で推進してきました.さらにJKAの競輪の補助を受けて, さらにこの研究を発展させ,ZM21マグネシウム合金について外径3.49mm,肉厚0.48mmの極薄肉管の創製に成功し,結晶組織制御による高耐食性も実現することができました.
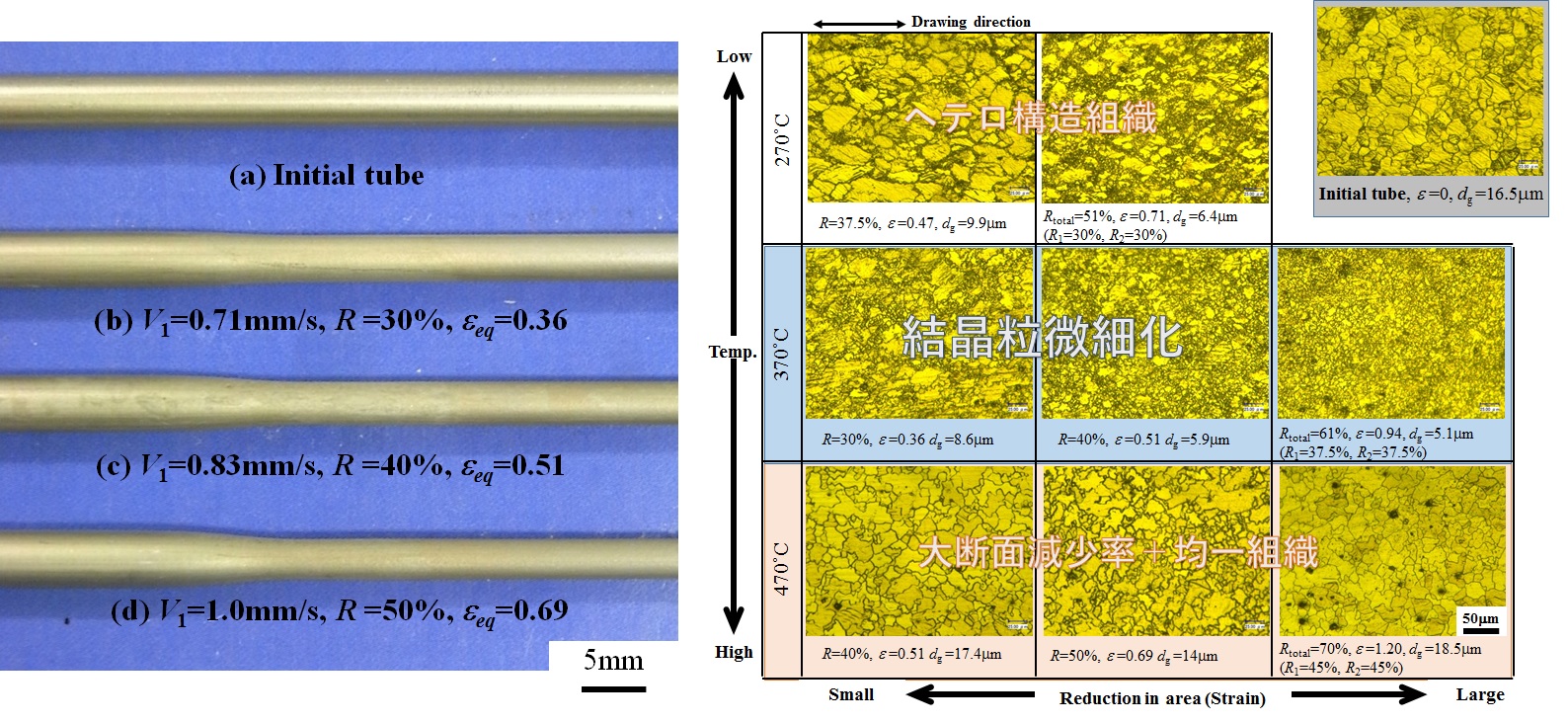
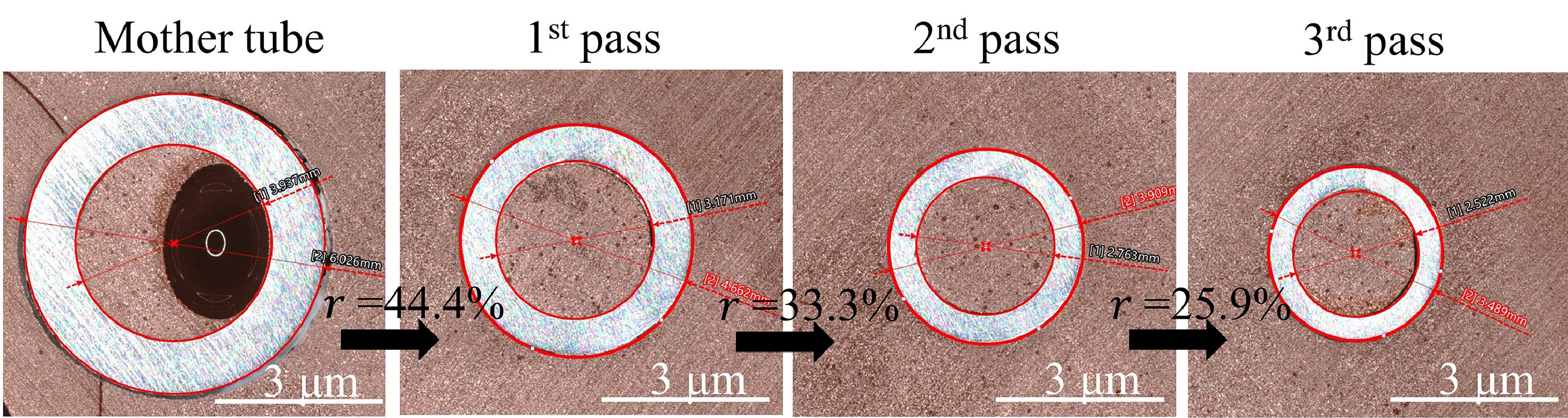
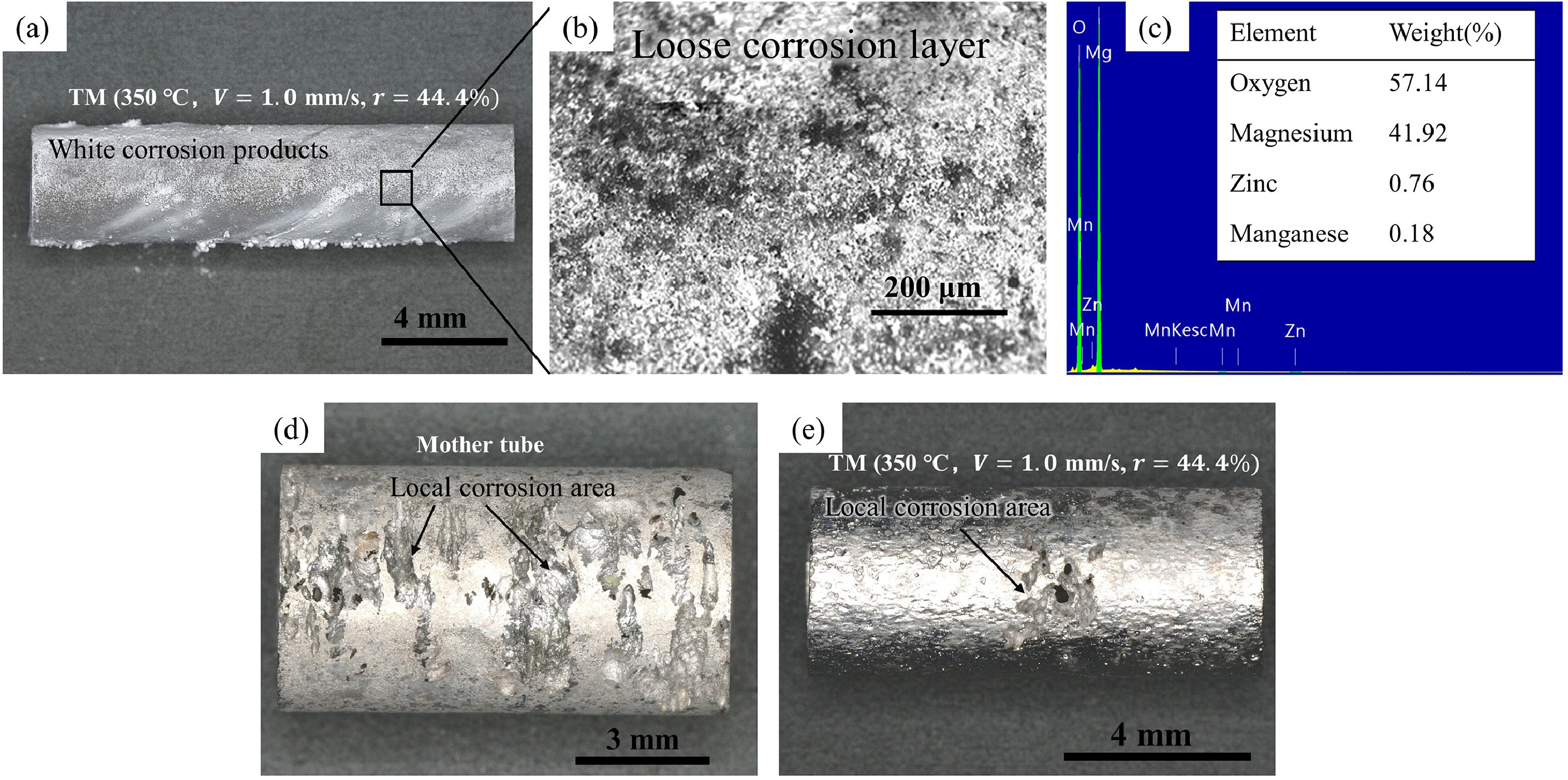
超塑性変形と破壊を利用した革新的ダイレス引抜きによる極小先端径を有する金属中空マイクロニードルの創製
近年,ライブセルアトラス(LCA)において,細胞1個を操作するツールとして極細先端径を有するマイクロニードルが望まれています. しかしながら,これまでマイクロニードルはガラス製であり,強度と脆性の観点から先端径数十ミクロンのガラス製マイクロニードルは応用が困難でした. そこでガラスに変わって強度と延性に優れた金属製のマイクロニードルが望まれていますが,先端径数十ミクロンの金属製マイクロニードルの創製はとても難しいものがあります. 本研究では,金属製マイクロニードルの創製にダイレス引抜きを応用した方法を開発しました. これまでのダイレス引抜きは,破断しないように安定した引抜きを行うことに主眼をおいていましたが,逆転の発想で,あえて破断させること先端径を一気に細くし,根本は1mmの径でありんがら,先端径が数十ミクロンの金属製マイクロニードルの創製しました. 本研究はJKAの競輪の補助を受けて実施しました.
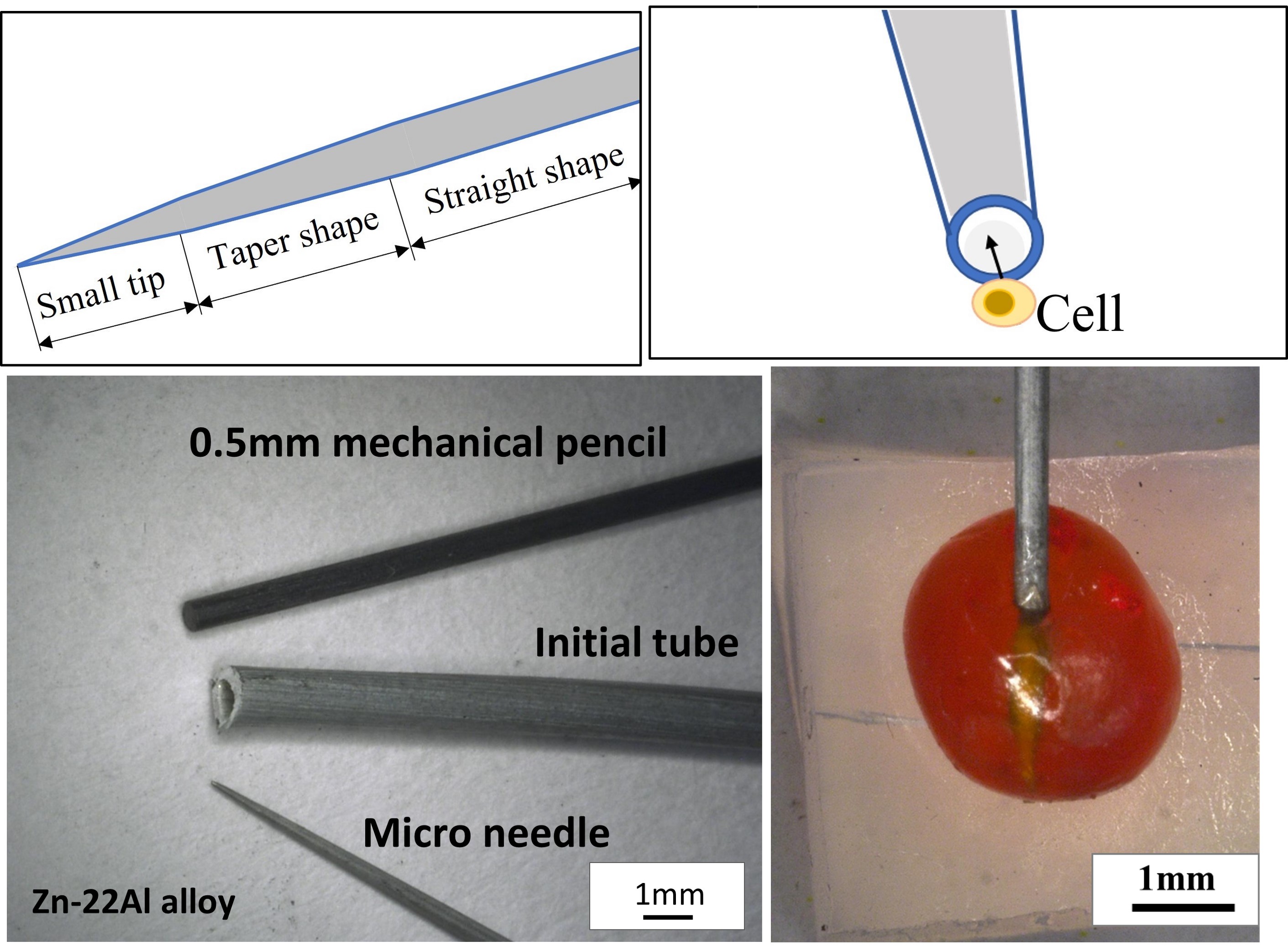
ダイレスベローズ成形に関する研究
金属管材を局部加熱しながら圧縮しながら加熱源内を移動させることで(ダイレス引抜きの引張とは逆の圧縮のモーション),座屈挙動を制御することによって,連続的に蛇腹形状を創製し,ベローズ状の形状を,金型を使わずに加工する方法を開発しています. また本手法を,レーザを加熱源にマイクロ化することでマイクロベローズをダイレスフォーミングにより創製することにも成功しています. 本研究は東北大学(中国)との共同研究です.
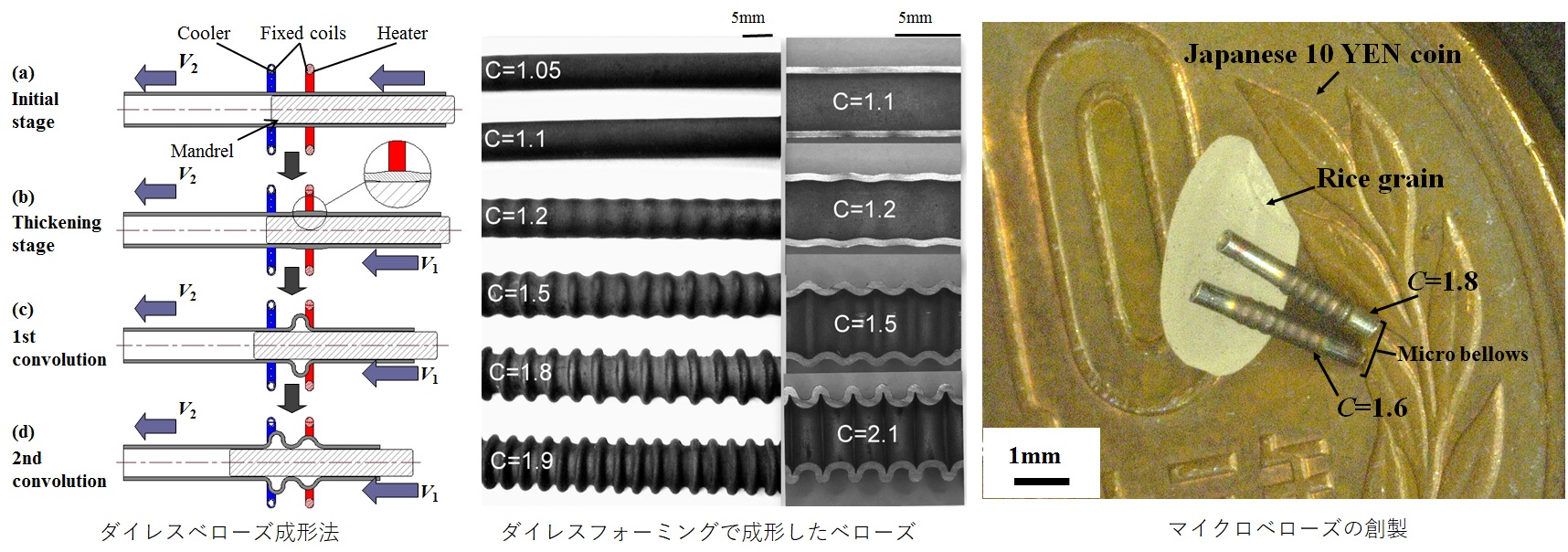
セラミックスチューブの超塑性ダイレスフォーミング成形に関する研究
近年,地球温暖化問題に関する温室効果ガス削減を達成する手段として,コンパクトかつ高効率なマイクロ燃料電池の開発が電気自動車の発展に必要不可欠です. 燃料電池の小型化するために,微細なセラミックチューブを内部に集積した角砂糖大の超小型の固体酸化物型燃料電池(SOFC)集積体を開発した事例があります. さらなるSOFCの小型化・高効率化を目指すにはより細いセラミックマイクロチューブを安価に大量生産する手法が必要です. 一般で気にセラミックは脆性材料ですが,1985年に若井らがセラミックの組織を微細粒状化すると高温域で数百~数千%の伸びが得られる超塑性現象が発生することを発見しました. その一方で,超塑性発現温度が1400~1700℃と非常に高温であるため,塑性加工で使われる金型では耐えることができず,実用化には未だに至っていないのが現状です. そこで本研究では,研究室にてこれまでに開発してきたダイレスフォーミングを超塑性ジルコニアセラミックチューブに応用し,アセチレンバーナを用いて1700℃の超高温加熱中に金型を用いずダイレスフォーミングをする手法を開発しました.
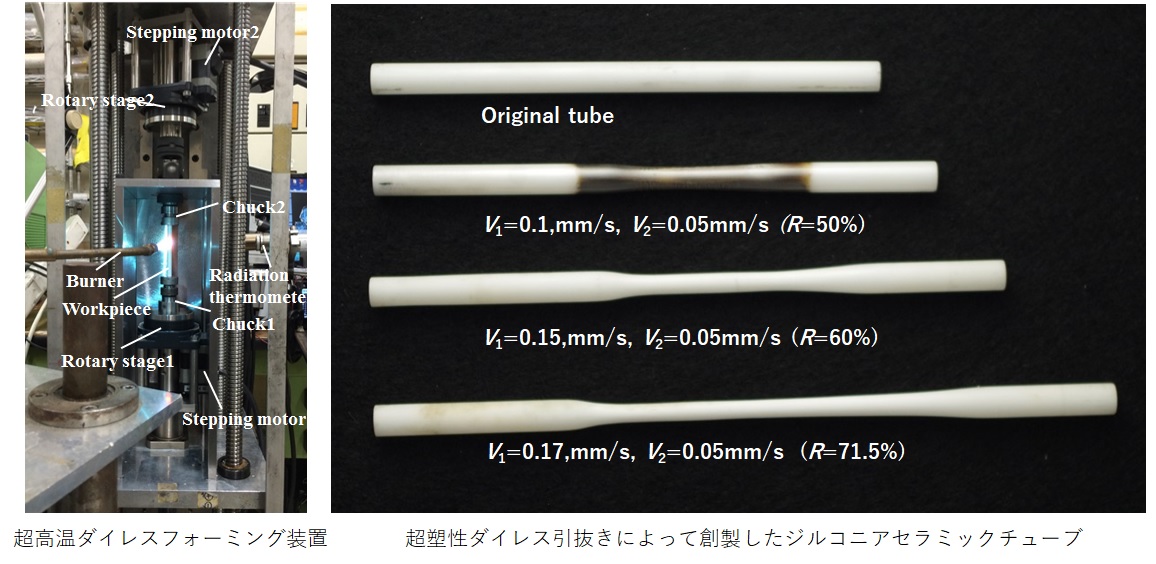
3. 塑性変形特性評価の高精度・高性能化
塑性加工の高精度化を実現するためにはシミュレーションの高度化が必須です.特に塑性変形特性を高精度に評価することは非常に重要です. 本研究では,特殊な評価技術を用いてこれまでにない新しい塑性変形特性評価手法を開発しその高精度・高性能化を目指しています.
レーザスペックルパターンを用いたデジタル画像相関法による完全非接触塑性ひずみの計測
デジタル画像相関(DIC)は,画像処理技術を用いてリアルタイムで変形された物体の対象領域(ROI)の変位及びひずみ分布を取得する方法として近年注目されています. 2枚の撮影した画像の相関性を計算するため,通常はサンプルの表面に塗料をスプレーし,人工スペックルパターンを作成する必要があります. しかしながら,塗料の剥がれにより,特に高温での大きな塑性変形における材料の変形挙動を取得することが難しくなります. また塗料厚さの影響で箔材のひずみを正確に評価できないという問題点も生じます. これらの問題を解決するためにレーザ光が物体の表面に照射された際,表面の微小な凹凸により散乱光が互いに干渉することで形成されるレーザースペックル現象に着目し, 本研究ではこれをDICに適用し,完全非接触の塑性ひずみ計測手法を開発しました.
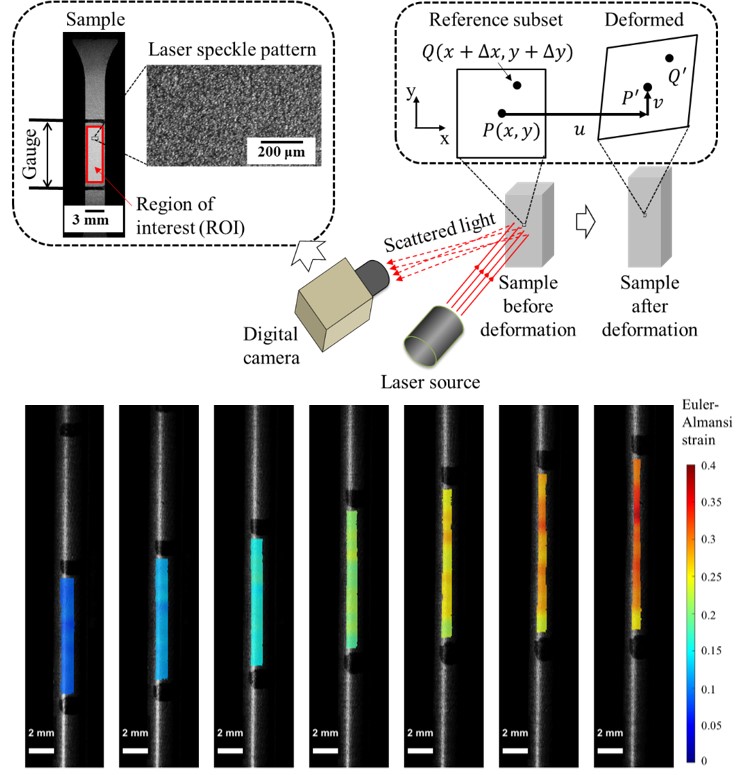